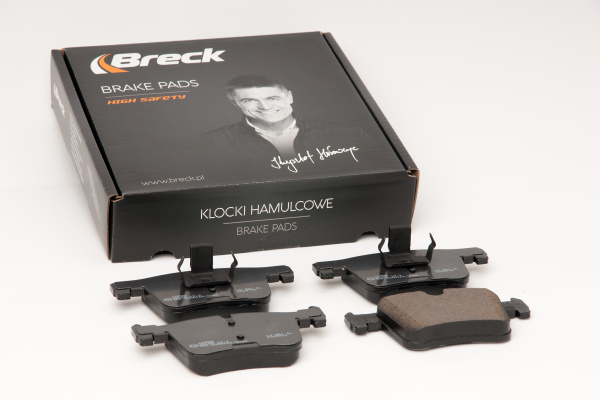
For many people, including many car enthusiasts, the matter is simple – what makes the vehicle stop is the braking system, with the main role played by brake pads and discs, significantly supported by tires. However, experts perceive this seemingly simple phenomenon as a complex physical and chemical process, in which the so-called third body layer (TBL) plays a crucial role.
It is mainly owing to the TBL that every brake pad manufacturer recommends driving calmly without sudden manoeuvres for a few dozen kilometres following brake pad replacement. This time is necessary not only for new components to break in, but also to allow the TBL to form. Excessive brake pad load without proper breaking-in can overheat and burn the pads, severely disrupting the TBL formation process.
“Third Body Layer – this mysterious term denotes a mixture of various substances and materials involved in the braking process. To use more technical terms, it is a layer of carbonised organic products, metal sulphides and oxides, and other nonreactive components of the friction material and of the brake raceway. It is formed during breaking-in of brake pads and brake discs. Small particles of the friction material and brake disc released during breaking-in are captured by surface irregularities of both interacting components. The resulting mixture has a different composition than the original parts, that is the brake pad and the brake disc”, explains Tomasz Orłowski, head of the Lumag’s Research and Development Department, tasked with the development of Breck brake pads.
During braking, TBL separates the friction material from the disc, protecting metallic components of the friction material from gluing together or fusing with the disc. This process involves phenomena, which experts call “adhesion” and “micro welding”. As long as the TBL exists, the friction coefficient remains stable, which directly translates into braking efficiency and, consequently, our safety.
“The key role in the formation of the TBL is played by components from the group of solid oils. Among other substances, it includes metal sulphides, graphite and petroleum coke. Solid oils can be perceived as solids, which lower friction and wear of components rubbing against each other. Temperature and pressure in the braking system are other factors influencing the formation of the TBL”, Tomasz Orłowski adds.
The TBL is destroyed, when large amounts of energy, mainly caused by high speed and high load, have to be dissipated, and when brakes are hot during braking. However, at the same time, this layer is gradually rebuilt and, after some time, it regains its properties. The individual driving style of every driver has a large influence on the TBL formation process as well.
“Driving calmly without excessive braking at high speed helps to maintain the properties of TBL in our vehicle. Dynamic driving leads to rapid degradation of the Third Body Layer and hinders its regeneration, lowering the efficiency of the braking system. The lack of a fully formed TBL during emergency braking can extend the braking distance by a few inches and, instead of stopping our car safely, we may cause a collision”, warns Tomasz Orłowski.
About the Breck brand
The Breck brand specializes in the manufacture of high-quality brake pads for passenger cars and commercial vehicles. It was created in 2003. Its portfolio covers over 500 products designed for various vehicle models. The brand offering is being constantly developed owing to the cutting-edge Research and Development Department. Breck products are made in one of the most modern friction material factories in Central and Eastern Europe located in Budzyń in the Greater Poland province. The in-house Compress Control system ensures that every product made in the production facility features the same high quality. Breck forms a part of the Lumag company, which sells over 8 million brake pads for passenger cars, commercial vehicles and trucks around the world every year.